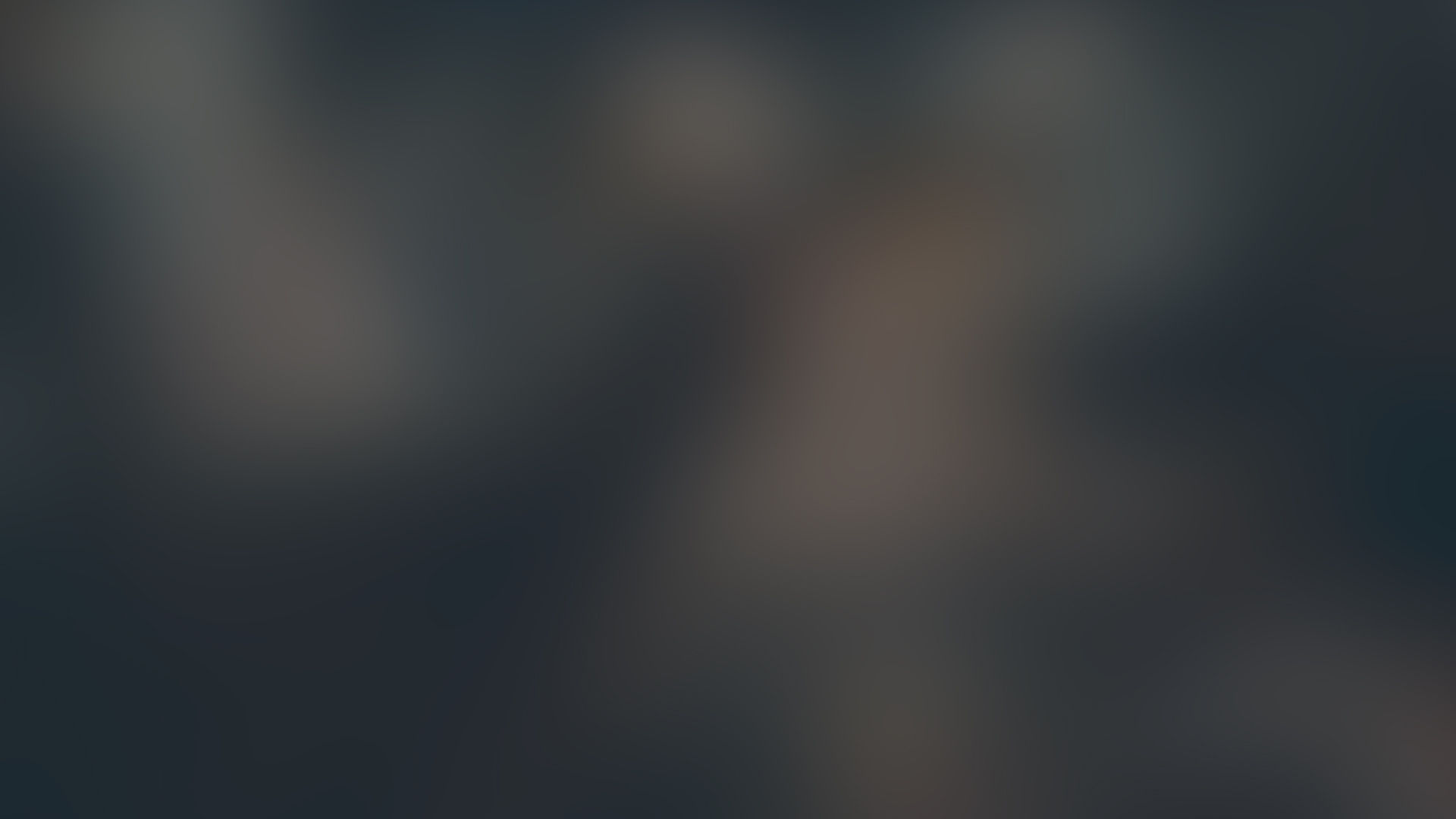

flow regulation
flow limitation
PID Control Flow, Control Valves

CONTENTS
1 - TYPE OF TERMINAL UNITS
A terminal unit is one that receives cold and/or hot water for the transfer of thermal energy to another medium, and there are two types depending on the secondary fluid:
-
Air-water:
-
Batteries:
-
fan coils
-
Air treatment units, UTA's
-
Evaporators
-
-
Radiators
-
-
Water water:
-
Heat exchangers, plate or tubular
-
coils
-
Internal cooling of a process, for example moldes
-
📢📢They all have one thing in common:
capacity regulation is carried out by varying the water flow, it does not matter if it is done by V2V or V3V. That is, on the side of the terminal unit, the flow rate is always variable.
2 - TYPES OF REGULATION
Depending on the type of regulation we have:
-
Static flow regulation or static balancing.
-
The flow is regulated in a fixed way, turning the actuator (its KVs is modified).
-
It is a seat valve with 2 pressure taps that allows the flow to be measured.
-
If the differential pressure on the valve changes, the flow rate changes
-
-
Flow limitation, regardless of differential pressure
-
It maintains the flow in any circumstance of differential pressure
-
They are made up of a cartridge and a spring that se moves depending on the pressure to keep the flow constant
-
Cannot measure flow on this valve
-
-
Dynamic flow regulation, closed PID control loop
-
Normally 2 or 3-way seat valves, with a motorized actuator (electric or pneumatic) and that responds to a control loop.
-
They are classified based on:
-
Opening or closing movement:
-
Linear: seat or gate
-
It has a cone-shaped seat and stem.
-
To regulate the flow, the stem opens and closes linearly.
-
They have a great flow regulation capacity; the flow is proportional to the opening percentage.
-
They are excellent for applications where precise flow control is required
-
-
Rotary: ball or butterfly
-
It has a ball with a hole.
-
To regulate the flow, the ball opens and closes by rotating it 90°.
-
They are fast acting, with a small opening percentage allowing the passage of a large amount of flow.
-
The pressure drop across the valve is very small.
-
Recommended for On/Off control applications
-
-
-
By the number of ports: 2 or 3 ways.
-
Depending on their position, the V3V can be diverting or mixing:
-
Mixers: allow proportional mixing of the inlet fluids through the direct route or port or through the "bypass".
-
Diverters: allow the flow of a fluid to be diverted, totally or partially.
-
-
-
For the control characteristic:
-
Quick opening
-
Linear
-
iso percentage
-
-
-
-
Automatic balancing, DPCV (Differential Pressure Control Valves)
It is a valve capable of maintaining constant differential pressure regardless of pressure variations in the circuit as a consequence of the opening and closing of the different V2V of a variable flow circuit._d04a07d8-9cd1-3239- 9149-20813d6c673b_


3 - VALVE CONTROL CHARACTERISTIC
1 - Quick opening:
When started from the closed position, a quick-opening valve allows a considerable amount of flow to pass for a small stem travel.
As the stem moves toward the open position the rate at which flow rate increases per stem movement decreases non-linearly.
This feature is used in two position or on/off applications.
2 - Linear:
Linear valves produce equal flow increments for equal stem travel throughout the entire range of stem travel.
This feature is used on steam coils and the bypass port of three-way valves.
3 - Equal percentage
This type of valve produces an exponential rise as the stem moves from the closed to the open position. The term equal percentage means that for equal increments of stem travel, the flow rate increases by an equal percentage.
For example, in the figure above, if the valve is moved from 50 to 70% of full travel, the percentage of full flow changes from 10 to 25%, an increase of 150%.
So if the valve moves from 80 to 100% of full travel, the percentage of full flow changes from 40 to 100%,
again, a 150% increase.
This feature is recommended for the control of hot and cold water terminals.
It is advisable to use a valve whose control characteristic is inverse to the thermal power emission curve of the terminal equipment which it is controlling:


Valves generally control the flow of fluids by means of an actuator, which moves a stem with a plug attached. The plug seats inside the valve port and against the valve seat with a composition disk or metal seat.
Depending on the plug geometry, three different flow conditions can develop
-
Quick opening
-
Linear
-
iso percentage
⚠️This compensation requires the fulfillment of two conditions ⚠️
👉 That the differential pressure on the control valve is constant.
👉 That the design flow is available at a fully open control valve.
If the differential pressure in the control valve is not constant, or if the latter is oversized, its characteristic will be distorted, compromising the modulating control of the loop. Is it important to stabilize the differential pressure?
4 - CONTROL VALVE AUTHORITY
The authority of a β valve is defined by the relationship between the pressure drop across it when fully open Δpmin (which is the minimum) and the pressure drop of the entire circuit affected by the valve or, what is same, the differential pressure across the valve when it is closed (at theoretically zero flow) Δpmax (which is the maximum, and which is equal to the pressure loss across the fully open valve plus the pressure loss across the other elements of the circuit in the same conditions of fully open valve):

Valve authority measures the extent to which the control valve is capable of imposing its characteristic on the circuit it controls.The greater the resistance of the valve, and therefore the pressure drop across it, the better the control valve will control the release of energy from the circuit.
Under actual operating conditions the ∆P across the valve does not remain constant, which means that the effective characteristic of the control valve changes.
The lower the authority of the valve, the greater the deflection and make sure it is as high as possible to minimize deflection.

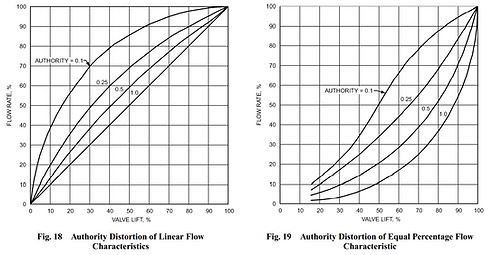
The value of authority β can vary from 0% to 100%.
A small value of β means a small pressure drop across the valve relative to the pressure drop across the entire circuit.
When β is small, the flow rate is predominantly determined by the pressure drop across the other circuit components, and valve opening or closing operations have little influence on the flow rate.
❌ This circumstance negatively affects the controllability of the system, precisely because the valve has little authority. If the authority is too small, the valve will have to work over a very small plug travel, which makes it difficult for the control loop to act.
❌ On the other hand, the maximum value of the authority must be limited to avoid excessive speeds of the water as it passes through the valve and, therefore, wear due to erosion and noise.
✅ To ensure correct operation of the valve, its authority must be equal to or greater than 0.5
5 - CHARACTERISTIC OF A CONTROL VALVE, KV and KVs
The flow coefficient (kv ) is a design factor that relates the pressure difference (Δp) between the inlet and outlet of the valve with the flow rate that passes through it.
The water flow depends on the differential pressure applied to the valve according to the following formula:
where, Kv is the flow factor of the valve, ρ is the density, (being for water, 1,000 Kg./m3 at 4ºC, 970 Kg./m3 at 80ºC), q is the flow in m3/h, and ∆p is the differential pressure expressed in bars.
The Kvs is the maximum kv for the fully open valve.
The control valve is selected so that its Kvs provides the design flow for the differential pressure available when the valve is working at nominal conditions.
It is not easy to determine the Kvs of a control valve, since the differential pressure available across the valve depends on many factors, including the following:
• Actual manometric head of the pump.
• Pressure losses in pipes and accessories.
• Load losses in terminal units.
• Head losses of the branch
These pressure losses also depend on the precision with which the hydraulic balancing is carried out. In the project, the correct theoretical values of the pressure losses and flows in the components of the installation are calculated. But components with the exactly specified properties are hardly to be found on the market.
Consequently, the installer must purchase standard type pumps, control valves and terminal units.
Control valves are available on the market with Kvs values that increase according to a geometric progression called Reynard series: Kvs: 1.0 1.6 2.5 4.0 6.3 10 16.....
Each value is approximately 60% greater than the previous value. It is not normal to find a control valve that creates exactly the desired head loss for the design flow.
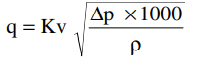

6 - SIZING OF A CONTROL VALVE

The required valve size is chosen in such a way that the calculated kv value for maximum demand is as close as possible to the chosen valve's Kvs value (but still lower).
Range Factor: Provides information on what is the minimum flow that the valve can control under stable pressure conditions.
The Kv coefficient for the fully open valve is called Kvs while the minimum value is called Kvr. The relationship between the two is called the control field or "rangeability" and expresses the flow rate that the valve can control while maintaining the inherent characteristic curve.

